Technical Specifications
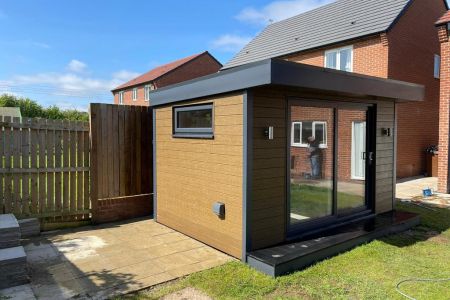
PVCu Door & Windows:
Each composite garden shed is supplied with a single anthracite (dark grey) 0.9m wide PVC-U entry door. Our composite garden pods are supplied with either a 1.5m wide set of French double patio doors or a 2.4m wide sliding patio door section and a wide opening window.
PVCu is a type of plastic material that is known for its durability, low maintenance requirements, and energy efficiency. Each door\s are constructed from a PVCu frame, which is reinforced with galvanized steel for added strength and security.
The high-quality anthracite profiles blend perfectly with any of the different external composite garden building cladding options. In addition, the dark grey profiles offer elegant sight lines together with high security features, incredible strength and thermal efficiency. The glass section used are A rated tinted Planitherm argon gas filled double glazed units.
Insurance Approved Locks:
Our individual aluminium reinforced PVCu single, double and sliding door sections are fitted with insurance approved locking mechanisms. This locking system offers a higher level of security than the standard five lever mortice deadlock, as it bolts the door into the door frame and has multiple locking points around the door section.
Insurance approved locks are locks that have been tested and certified by independent organizations to meet certain security standards set by insurers. These locks are designed to provide a higher level of security and are often a requirement for insurance policies covering high-value items.
Timber Frame Construction:
All our composite garden buildings are manufactured using traditional timber framed walls and floor. Timber frame construction is a traditional method of construction that has been used for centuries and is still used today for both residential and commercial buildings. In timber frame construction, the timber frame acts as the primary structural support for the composite garden shed.
The composite garden shed walls are constructed using solid 75mm structural graded timber and the floors are constructed from 100mm structural graded timber frames to carry the load of the building. The floor timbers are pressure treated and impregnated with Tanelith E wood preservative.
The composite garden pod walls are constructed using heavy duty solid 100mm structural graded timber and the floors are constructed from 120mm structural graded timber frames to carry the load of the building. The floor timbers are pressure treated and impregnated with Tanelith E wood preservative.
The internal timber floor carcase of both the sheds and pods is completely covered using an 18mm industrial grade moisture resistant tongue and grooved timber floor boarding.
Inside our quality composite garden buildings, you will find all the walls lined with 11mm OSB timber. Oriented strand board (OSB) is an engineered timber board which has superior strength than plywood and is ideal for the inside of a garden building.
High Performance Breathable Membrane:
The composite garden building walls are wrapped in a specialist high performance waterproof breathing membrane. A waterproof breathable membrane is a type of material that is used in building construction to protect buildings from moisture while allowing water vapor to escape.
The membrane is made up of a thin layer of microporous material that is designed to be both waterproof and breathable. This allows moisture to escape from the composite garden shed or pod, while preventing water from penetrating the membrane.
One of the advantages of a waterproof breathable membrane is that it can help to prevent the build-up of condensation within the walls or roof of the composite garden shed or pod. This can help to reduce the risk of mould growth and other moisture-related problems.
Another advantage of a waterproof breathable membrane is that it can help to improve the energy efficiency of the composite garden building by reducing the amount of heat loss through the walls or roof. This can help to reduce heating and cooling costs over time.
Our composite garden shed and pod structures additionally incorporate double vented timber walls allowing air to circulate, enabling the structure to breathe.
Fully Insulated Roof, Walls and Floor:
A fully insulated roof, floor, and walls refer to a building that has all of these elements insulated in order to prevent heat from escaping during the colder months and to keep the space cool during the warmer months. This helps to reduce energy costs and make the building more comfortable to live or work in.
The composite garden shed structural timber floor and wall sections contain 50mm Knauf RS45 thermal acoustic insulation and the roofs are constructed using a 40mm profiled fully insulated trapezoidal roof panel. These insulated interlocking roof panels are supplied Anthracite (dark grey) on the outside and white on the inside.
The composite garden pod structural timber floor and wall sections contain 75mm Knauf RS45 thermal acoustic insulation and the roofs are constructed using a 100mm profiled fully insulated trapezoidal roof panel. These insulated interlocking roof panels are supplied Anthracite (dark grey) on the outside and white on the inside.
The insulation material is installed between the wall studs, and a vapor barrier is used on the exterior walls to prevent moisture from getting inside the walls or ceiling.
When a building is fully insulated, it can significantly reduce the amount of energy needed to heat or cool the space, which can result in lower energy bills and a more comfortable indoor environment. Additionally, a well-insulated building can help to reduce greenhouse gas emissions and contribute to a more sustainable future.
Fibre Cement Boarding:
Fibre cement composite cladding is a type of building material that is commonly used for exterior cladding. It is made by combining cement, sand, and cellulose fibres to create a durable and weather-resistant material.
Fibre cement boards are a high-quality, low-maintenance and water-resistant cladding solution that have been manufactured to withstand harsh weather conditions with little expansion or contraction.
One of the benefits of fibre cement composite cladding is its durability. It is resistant to moisture, insects, and rot, which makes it a low-maintenance option for building exteriors. It is also eco-friendly, as it is made from natural materials and can be recycled at the end of its useful life.
Fibre cement boards are available in a range of colours as well as an unpainted option, allowing you to create your desired look with ease. Colours include: Cream, Sage Green, Slate, Granite, Light Grey, Black, Blue, and White.
Smooth Composite Cladding:
Smooth composite cladding is a type of cladding that is used on the exterior of buildings to provide a sleek and modern appearance. Manufactured using a combination of 60% recycled hardwood fibres and 40% recycled plastic, our smooth composite cladding is zero maintenance and insect and rot resistant. Unlike traditional timber cladding, our smooth composite cladding does not require staining, varnishing or sanding throughout its lifespan.
The smooth surface of composite cladding provides a uniform appearance, without the natural variations found in wood. Available in a range of eight composite colours - Redwood, Olive Green, Ivory, Teak, Coffee, Charcoal, Light Grey and Stone Grey.
One of the benefits of smooth composite cladding is its low maintenance requirements. It is resistant to rot, insect infestation, and fading, and does not require painting or staining. It is also lightweight and easy to install, making it a popular choice for both new construction and renovation projects.
Woodgrain Composite Cladding:
Woodgrain composite cladding offers the aesthetic appeal of natural wood without the maintenance requirements. It is available in a variety of colours and finishes, including a range of wood tones and textures, to complement different architectural styles.
One of the benefits of woodgrain composite cladding is its durability. It is resistant to moisture, rot, and insects, and does not require painting or staining. This makes it a low-maintenance option for building exteriors. Additionally, woodgrain composite cladding is eco-friendly. It is made from recycled materials and can be recycled at the end of its useful life. This makes it a sustainable choice for building exteriors.
Woodgrain composite cladding allow you to effortlessly achieve a wood cladding look on your exterior garden shed walls. The woodgrain texture gives a natural wood effect. Again, manufactured using a combination of 60% recycled hardwood fibres and 40% recycled plastic, our woodgrain composite cladding is zero maintenance and insect and rot resistant.
One of the benefits of woodgrain composite cladding is its durability. It is resistant to moisture, rot, and insects, and does not require painting or staining. This makes it a low-maintenance option for building exteriors. Available in a range of eight composite colours - Redwood, Olive Green, Ivory, Teak, Coffee, Charcoal, Light Grey and Stone Grey.
Slatted Composite Cladding:
Slatted composite cladding is manufactured from an innovative capped composite material that is environmentally friendly, Slatted Panels replicate the look of individual timber slats. Sometimes referred to as Shadow Gap Cladding, Slatted Cladding Panels can be installed either horizontally or vertically and create a stunning exterior look for garden building.
Manufactured using a combination of 60% recycled hardwood fibres and 40% recycled plastic, our slatted composite cladding is zero maintenance and insect and rot resistant. An excellent zero-maintenance option for building exteriors. Available in a range of six colours - Walnut, Teak, Stone Grey, Coffee, Charcoal and Silver Grey.
Delivery & On-Site Installation Included*
All our prices include the delivery and complete on-site construction by fully trained professional installation teams. Each composite garden building is installed with the minimal of disruption, typically within 1-4 working days (dependent upon size) and normally without the need for planning permission.
* Delivery and on-site is included within mainland UK. Unfortunately we do not install or sheds or pods in Northern Ireland or any areas outside of the UK.
Site Area
In order for us to construct your new composite garden building on site we need the construction area to be clear of any old buildings or sheds, trees, rocks and shrubs etc.
When constructing our buildings, it is important to choose a suitable location that is level and has proper drainage. This helps to ensure that the building is stable and durable, and prevents any water damage or drainage issues.
If the site area is not solid or entirely level we can offer a concrete pile foundation base system for the composite garden shed base at an additional cost - please contact us for pricing.
Composite Garden Sheds And Pods Permitted Development Rules
Outbuildings (including composite garden sheds and pods) are considered to be permitted development, not needing planning permission, subject to the following limits and conditions:- No outbuilding on land forward of a wall forming the principal elevation.
- Outbuildings and garages to be single storey with maximum eaves height of 2.5 metres and maximum overall height of 4 metres with a dual pitched roof or 3 metres for any other roof.
- Maximum height of 2.5 metres in the case of a building, enclosure or container within two metres of a boundary of the curtilage of the dwelling house.
- No verandas, balconies or raised platforms.
- No more than half the area of land around the "original house"* would be covered by additions or other buildings.
- In National Parks, the Broads, Areas of Outstanding Natural Beauty and World Heritage Sites the maximum area to be covered by buildings, enclosures, containers and pools more than 20 metres from house to be limited to 10 square metres.
- On designated land* buildings, enclosures, containers and pools at the side of properties will require planning permission.
- Within the curtilage of listed buildings any outbuilding will require planning permission.
* The term "original house" means the house as it was first built or as it stood on 1 July 1948 (if it was built before that date). Although you may not have built an extension to the house, a previous owner may have done so.
* Designated land includes national parks and the Broads, Areas of Outstanding Natural Beauty, conservation areas and World Heritage Sites.
Please note: The permitted development allowances described here apply to houses not flats, maisonettes or other buildings.